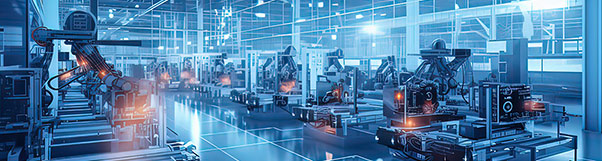
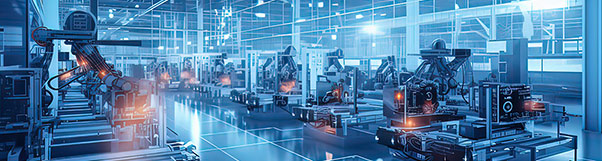
The global Machine Vision market size was valued at 13.23 B€ in 2021 and it is expected to expand at a compound annual growth rate of ~7 % from 2022 to 2030, with Europe accounting for about one-third of the total market revenue share. The rapid growth and innovation in Machine Vision Systems (MVSs) has brought a wave of industrial applications in many manufacturing sectors (e.g. aeronautic, pharmaceutical, medical, electronics, semiconductors).
For quality control, MVSs use cameras and sensors to analyse images, to monitor the quality of the product, and to report in-process deficiencies in quasi real-time. The deployment of Traceable-MVSs is perfectly aligned with zero-defect manufacturing and zero-waste ambitions. The intensifying need for superior inspection and increasing automation are the key influencing factors paving the way for the notable adoption of MVSs. The need for increased quality control by consumers and manufacturers, coupled with government regulations to abide by the prescribed specifications, is expected to catapult the future use of MVSs.
As the quality assurance and inspection segment held the largest revenue share of over 50 % in 2021, the availability of a traceable metrology for MVSs becomes indispensable for digital transformation in the Industry 4.0 strategy (a pillar of the EU Green Deal). Currently, calibration methods, including the measurement uncertainty of known influence factors, and approaches to identify additional contributions to the measurement uncertainty are still lacking. These are essential to optimise performances, allow validation, and to ensure metrologically reliable results, which could be enhanced through DTs based on physical or/and data AI-driven models. Nevertheless, the number of contributors addressed, and the methods used for their inclusion in Digital Twin (DT) models are currently very limited. For every developed DT, verification and validation are fundamental.
The published ISO10360-13:2021, has taken inspiration from the VDI/VDE 2634, and it addresses the traceability of optical 3D Coordinate Measuring Machines. This normative standard uses two spheres, which are traceable to the unit of length, the metre. Nonetheless, material standards with prismatic and complex shapes, which would be better related to industrial needs, are lacking. To support the implementation of ISO10360-13, additional materials standards need to be developed, which will provide traceability to MVS with validated DTs for assessing systematic errors and determining robust measurement uncertainties. In addition, reference dense matching algorithms are needed for merging recorded images into one coordinate system. To support the dissemination of this project’s results, industrial use cases related to dimensional, structural, surface and operational qualities and best practice guidance, and user training, seek to reinforce the deployment of MVS in Industry 4.0 processes.
The overall aim of this project is to generate traceability for the Machine Vision Systems (MVSs) that are deployed in industrial applications including macro- and microscale products based on the development of traceable material standards, V-DTs, uncertainty evaluation methods, robust and reliable dense-image matching algorithms, as well as robust classifiers and analysing algorithms.